Sanded aileron ends, repaired cracked rudder | 11.28.2020 - 11.30.2020
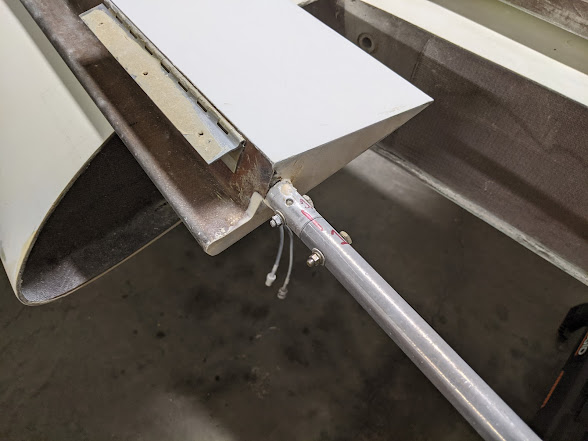
Started the night by sanding the aileron ends so that they were smooth and to help with fit in cutout. Also connected the torque tube to the aileron. Once that was done, I moved on to repairing a crack one of the rudders. I noticed this crack when inspecting the rudder a while back. I don't have a picture of it, but the crack was a pretty small ~5 inch hairline along the edge where the glass extends past the foam edge of the rudder (the front rib, basically). I put this off because I thought that I was going to need to repair the underlying glass and wasn't looking forward to it. I used a scraper to break off the micro-balloon where the crack was to see what needed to be done, and was pleasantly surprised to find that there was no underlying damage or de lamination. It seems like something just flexed that edge too far and cracked the micro-balloon layer on the rudder surface. I removed all the loose micro and beveled the edge to transition the secure micro down to the unde...