ELT hardpoint and canard tip layups | 12.27.2020
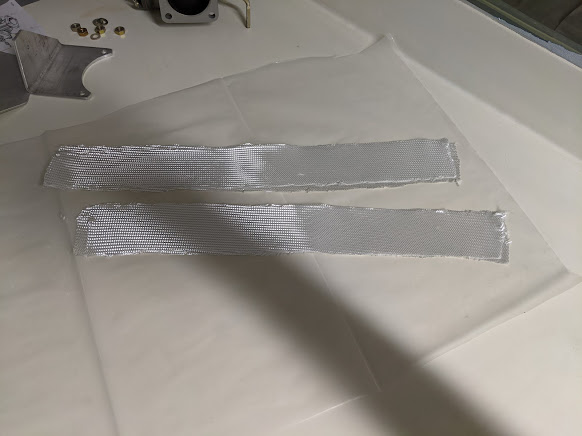
Did the layups on the ELT hardpoints and canard tips. Glass cut to size. 2 plies bid The manual calls for a single ply of bid here, but there was room for two plies with the thickness, so I just did two. Theoretically this will be stronger, but I doubt it's needed. I just wasn't so sure about the structural adhesive being the only thing holding it on really. Left tip Right tip The ELT hardpoints were potted with micro and then glassed over with two plies bid. That's all for now! - Jeff